H2PAD Manufacturing Process
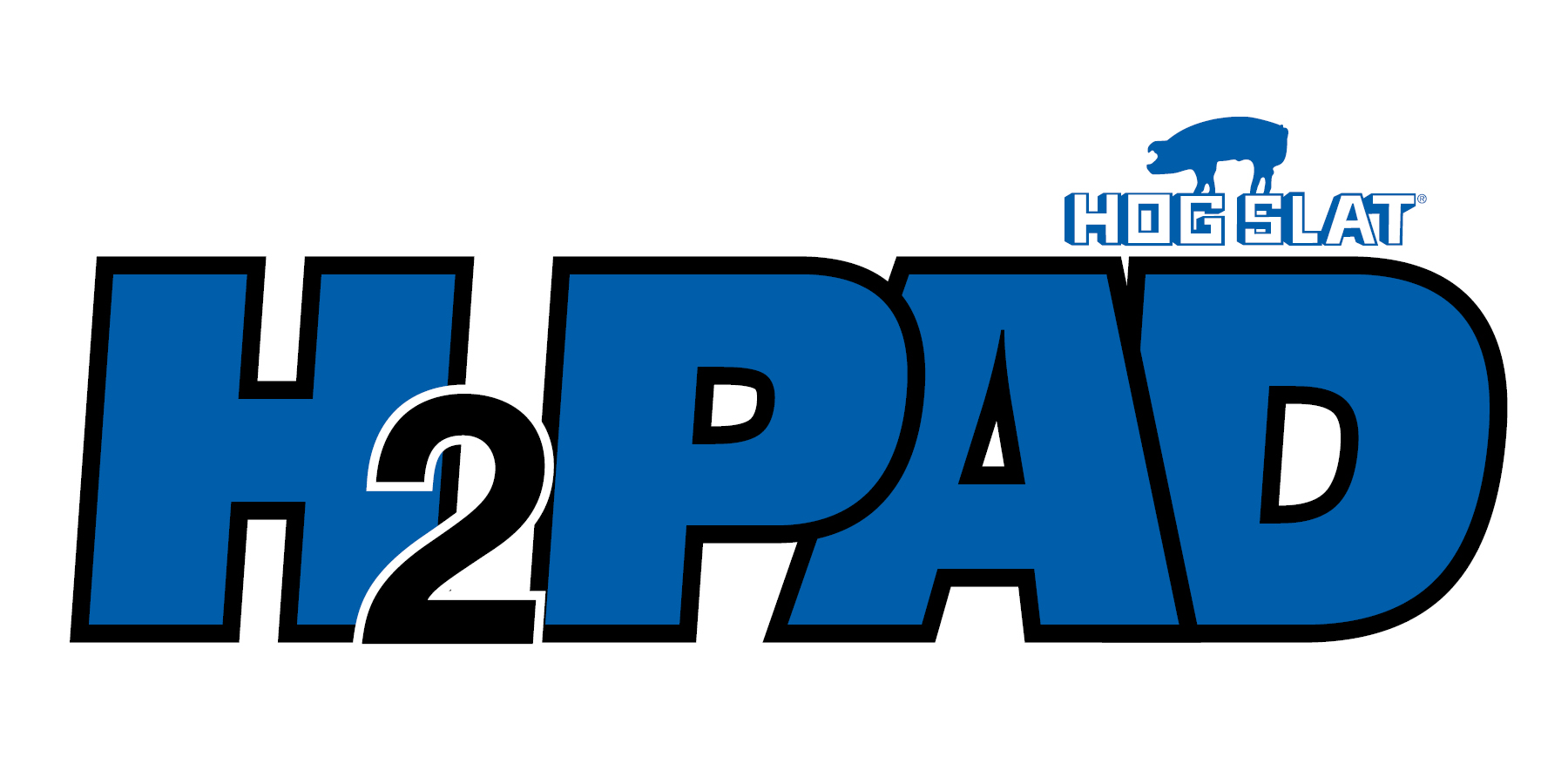 | Choose H2PADs in new systems and for replacements in existing cool cell systems. Manufactured with strict quality control to assure long life in the toughest conditions. Standard configuration includes 6" thick by 12" wide with 15/45 fluting and 3/4" ProTech coating on one side. Available in standard height options between 24" and 72" tall. Also available with optional two inches of ProTech on pad bottom. |
|
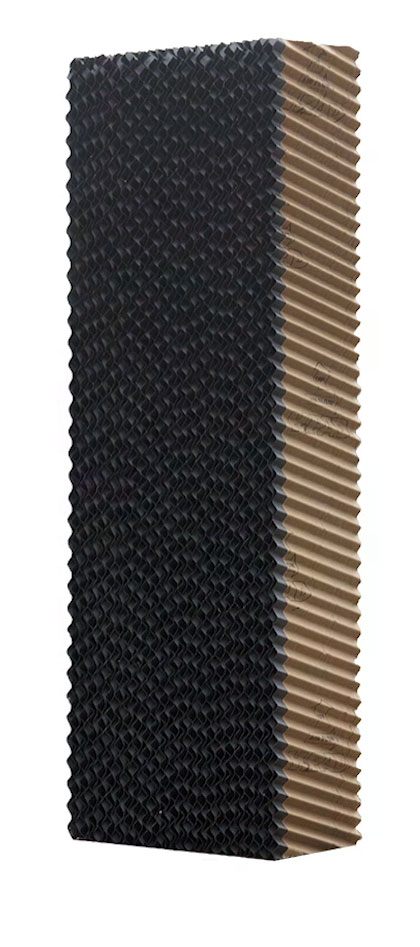 | 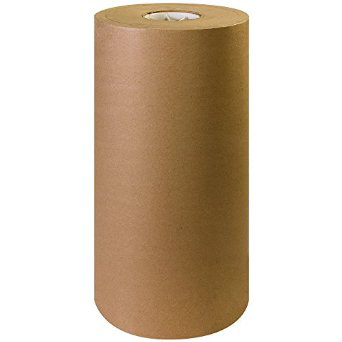 | Production of H2PAD begins by selecting heavyweight Saturation Grade quality cellulose Kraft paper, oven-cured with acrylic polymer glue and fungicides for superior cooling performance, increased lifespan and high water absorption rates. This specialty Kraft is also formulated for consistent resin pick-up; a crucial step to ensure proper resin impregnation during manufacturing. quality cellulose paper, oven-cured with acrylic polymer glue and fungicides for superior cooling performance and increased lifespan | 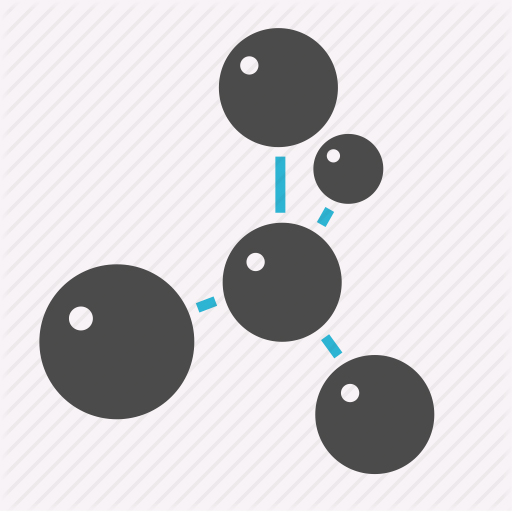 | A proprietary resin contains critical formulation of acrylic polymer glues, melamine additive for fire resistance, and fungicide additive. A special viscosity additive ensures even application on each sheet. | 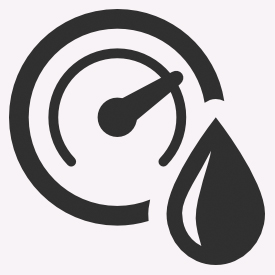 | Throughout the manufacturing process, technicians constantly monitor the moisture content of the paper. Consistent moisture content is critical to proper adhesion of glues and the curing process. | 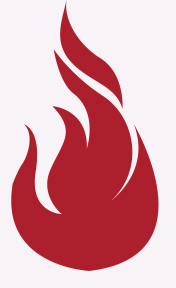 | Triple Curing Process. The first oven bakes the resin coating on the paper. The second oven cures each sheet individually after corrugating and before pressing to ensure consistent glue contact points. A third oven cures each media block for three hours before cutting and sanding. |
---|
|
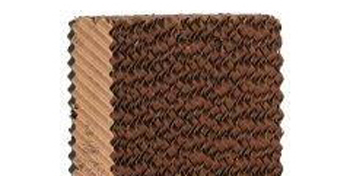 | 3/4” ProTec Edging increases pad life by protecting against UV light and mechanical damage when cleaning. Helps to prevent the buildup of algae and minerals on the air entry side of the H2PAD. Special wetting additive promotes even water distribution by reducing the amount water collecting on the pad surface. |
|
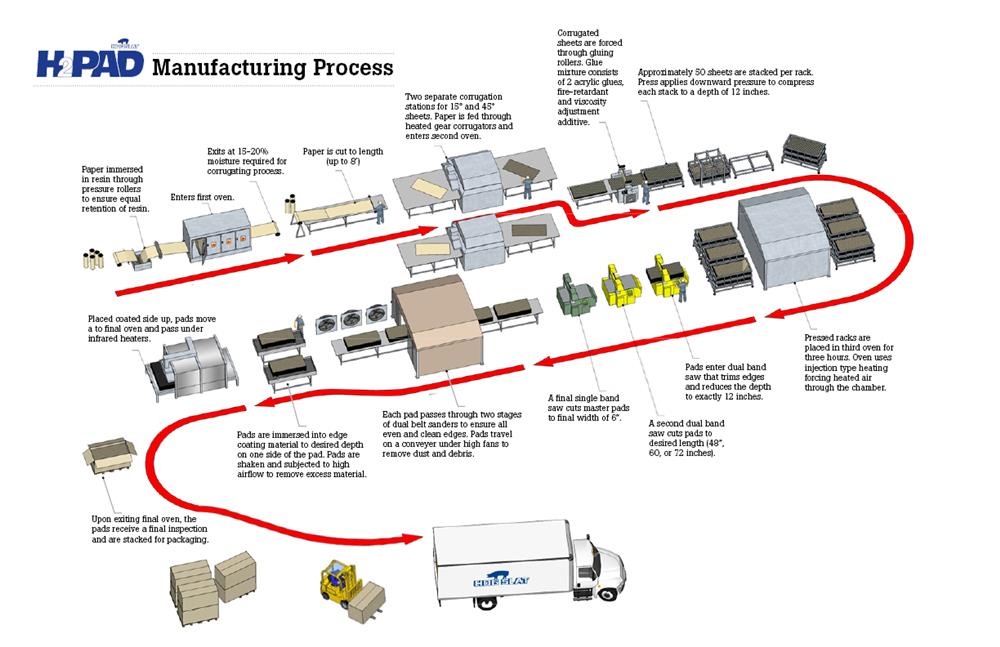 |
---|