The Lein family’s start in the egg business began with 12 hens back in 1999. Those hens provided eggs for the family as well a few neighbors and friends. Visitors to farm thought the hens had it so good they referred to them as “yuppie chickens”. When Lynn started direct marketing eggs she adopted the brand name, Yuppie Hill Poultry. As the business grew, Lynn acquired the present farm on Potter Road and converted an existing dairy barn into a laying house for 3,000 hens.
“That first house was a lot of work. We gathered the eggs, washed them and did the feeding all by hand. The air quality was poor and production never got above 70%” remarked Lynn.
In 2008, the family decided to increase production by constructing a new 50’ x 250’ flat deck house for 9,000 hens. Although the new system saved labor with automated feeding and egg gathering, the family researched other options before their next stage of expansion.
As Jay explained, “We were not totally satisfied with our conventional deck system. We felt the environment could be better for the chickens. In addition, we were spending a lot of time cleaning out the building between groups. The extended down time between groups made it hard for us to supply our customers and reduced our income.”
Their research led them to Potter’s Poultry, one of the leading manufacturers of cage-free production systems. After contacting Hog Slat rep Jason Billings, the group traveled to England to see firsthand the Potter’s System in use.
“We visited six commercial farms in four days and came away very impressed.” said Lyn “We were particularly interested in an aviary type system because the zoning restrictions on our farm forced us into putting as many chickens as possible in a limited floor plan. The other aviary systems we had looked at were really just big cages. Potter’s has been building aviary systems for 20 years and has designed a true cage-free system that is the most open one on the market.”
Jay added “We liked what we saw and came home determined to copy the style of barns we had seen in England. The ventilation was excellent and it equipment was built extremely heavy with a lot of small features that make a big difference.”
After returning, plans were finalized on 55’ x 245’ building with a center wall running the length of the building creating two individual rooms each capable of holding 8,900 hens. By combining this capacity with the first building the Leins will have three separate flocks. Because no more than one room is ever out of production for cleaning, eggs are always available to supply customers. Construction began in mid July and the first hens were placed October 3rd.
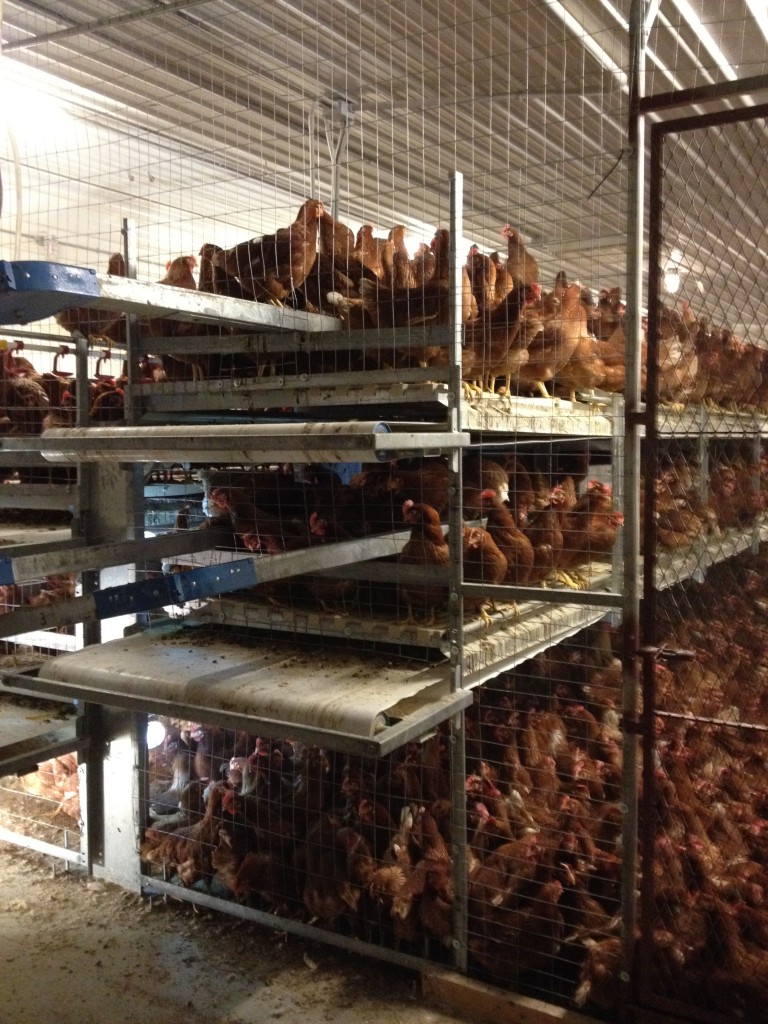
Colony nests are stacked two high along the center wall with the aviary facing it. The AVINEST colony nests allow hens to gather in groups behind privacy curtain to lay their eggs. The system uses the original AstroTurf pads that are perforated to allow dirt to fall away ensuring cleaner eggs. Cleaner eggs are also promoted by the automatic expulsion feature where the nest floors are lifted with a rack and pinion system gently moving the hens out of the nests at night time.
The aviary features perches where feed and water are available on multiple levels. Two manure belts also run the length of the system. On the other side of the aviary, opposite the nests, is a scratch area with doors that can be opened to an outside run. The computer controlled ventilation system features chimney style fans linked with automated sidewall vents.
When I asked about the different lights installed in the building Jay explained “First the red lights above the boxes come on at 4:00 until 6:00 am with the nests’ floors dropping down to provide access to the nests. At 5:30 the whole house fluorescents come on dim and gradually increase every 15 minutes until they are on full power. Next the perch lights come on, then the lights on the second layer of the aviary come on and finally the floor lights are activated. The floor lights are key to preventing floor eggs from being laid. At night the order is reversed with boxes closing around 4:00 pm with the house lights going down at 7:00. At 8:10 the bottom lights are turned off, the middle lights at 8:20 and the house lights are shut off at 8:30. This entire sequence is automatically controlled by a master light control.”
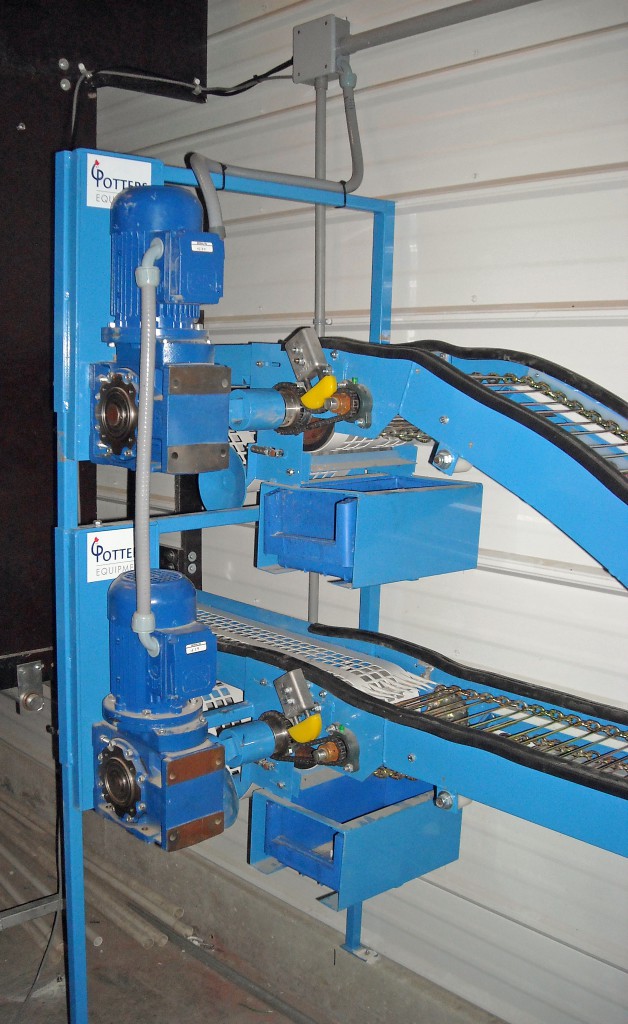
Egg collection system on the two-tier nest system is accomplished by the use of curved mini steel rod conveyers that bring the eggs to a single level. From there another conveyer system moves the eggs to collection area where the eggs are inspected, packaged and cooled until delivery to customers.
Jay also called out the manure handling belts. “We feel that one of the biggest benefits of this system over our older building is the ability to remove the manure frequently. Because a majority of the manure is deposited under the aviary perches, we are able to run the belts located under the aviary and dump them on to a cross belt where it is piled outside.”
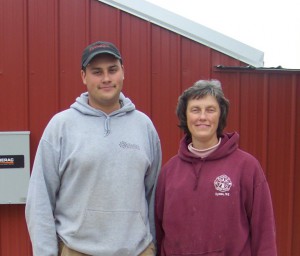
“We like our niche in the market” Lynn said when we discussing Yuppie Hill’s customers. “We supply upper-end restaurants and grocery stores in Madison, Chicago and Sheboygan. We provide a quality product produced by a family farm. Demand keeps growing and this new facility will enable us do a better job supplying our customers.”
One final point of interest at Yuppie Hill farm is the original dairy barn used for the first laying house has been converted again…into a restaurant that serves brunch every Sunday morning except the second weekend the month. The second weekend is devoted to special Saturday night theme dinner of four to five courses with neighborhood chefs invited in to host the event. The chefs prepare local foods paired with regional wines and beers. The event is becoming quite popular with the last couple of dinners being completely sold out.